“钢铁巨兽”驶入氢时代,年产5000辆!
氢能重卡规模化时代开启:探秘全国首条量产线落地
在工业机械的轰鸣声中,一台台氢燃料电池驱动的重型卡车从崭新的生产线上缓缓驶出。这座位于大同的工厂,刚刚创下年产5000辆氢能重卡的里程碑,标志着我国首条氢能重卡专用生产线正式迈入规模化生产阶段。这一突破不仅填补了国内氢能重卡量产空白,更以“零碳排放”的工业基因,为传统物流运输业注入绿色动能。

从实验室到流水线:技术自主化的关键一跃
氢能重卡的核心在于燃料电池系统,其技术曾长期受制于海外专利壁垒。而大同生产线的投产,首次贯通了从电堆研发、动力系统集成到整车装配的全链条自主化流程。以“氢燃料电池电堆全自动化生产”为代表的技术升级,将单套系统成本降低约30%,生产效率提升近4倍。
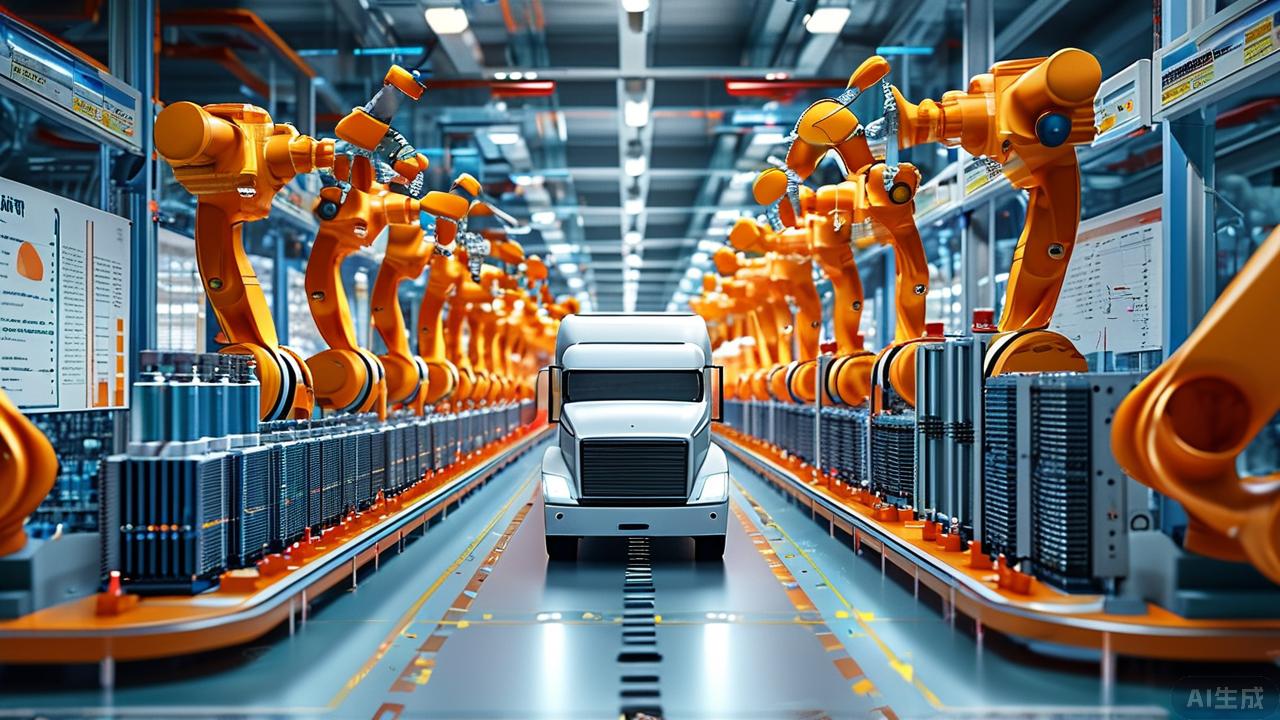
值得关注的是,生产线采用柔性化设计,可同时适配物流重卡、工程机械等多类车型。这种“模块化”思维,如同乐高积木般灵活组合,为氢能车辆跨场景应用预留了技术接口。正如业内人士所言:“这不仅是生产线的落地,更是氢能工业标准体系的奠基。”
经济效益与环保价值的双重跃迁
年产5000辆的规模效应,正在重构区域经济版图。以单台重卡售价150万元估算,该生产线年产值已突破75亿元,而配套的制氢、储运、加注等环节,更将带动全产业链向300亿元总产值冲刺。大同市焦炉煤气制氢技术的成熟,让每公斤氢气成本控制在25元以内,相比燃油重卡,氢能重卡每百公里运营成本下降近40%。
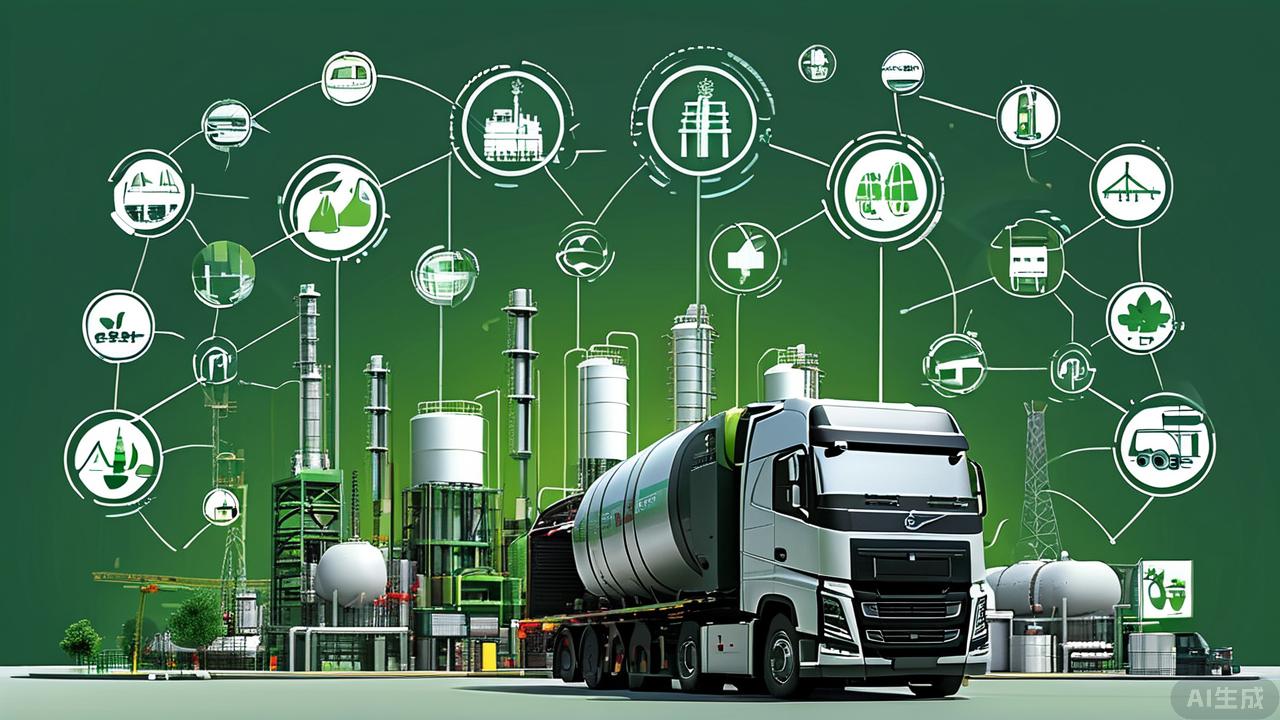
环保效益则具象化为一组震撼数据:5000辆氢能重卡全年可减少二氧化碳排放约150万吨,相当于再造8.5万亩森林的碳汇能力。当这些“钢铁巨兽”驰骋在西部陆海“氢走廊”时,1150公里的干线沿途,再不见黑烟尾气,唯有水蒸气凝结的薄雾掠过青山。
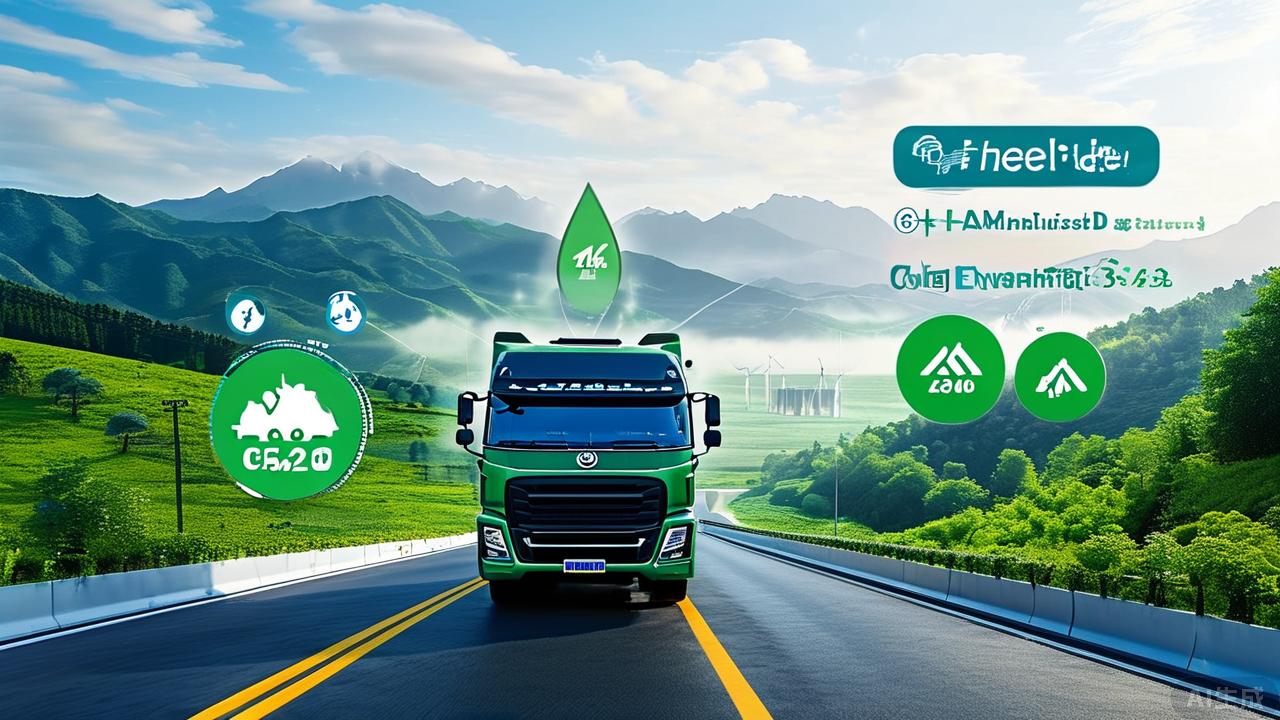
产业生态圈:从单点突破到网状协同
生产线的爆发式增长,背后是氢能基础设施的同步跃进。目前全国已建成加氢站超50座,其中12座密集布局在大同周边,形成“15分钟加氢圈”。晋南钢铁集团等链主企业,更创新“制氢-炼铁-车辆运营”闭环模式:焦炉煤气提取的氢气既用于氢能炼铁降碳,又通过自建加氢站反哺重卡车队,实现“氢流”在产业链内的内循环。
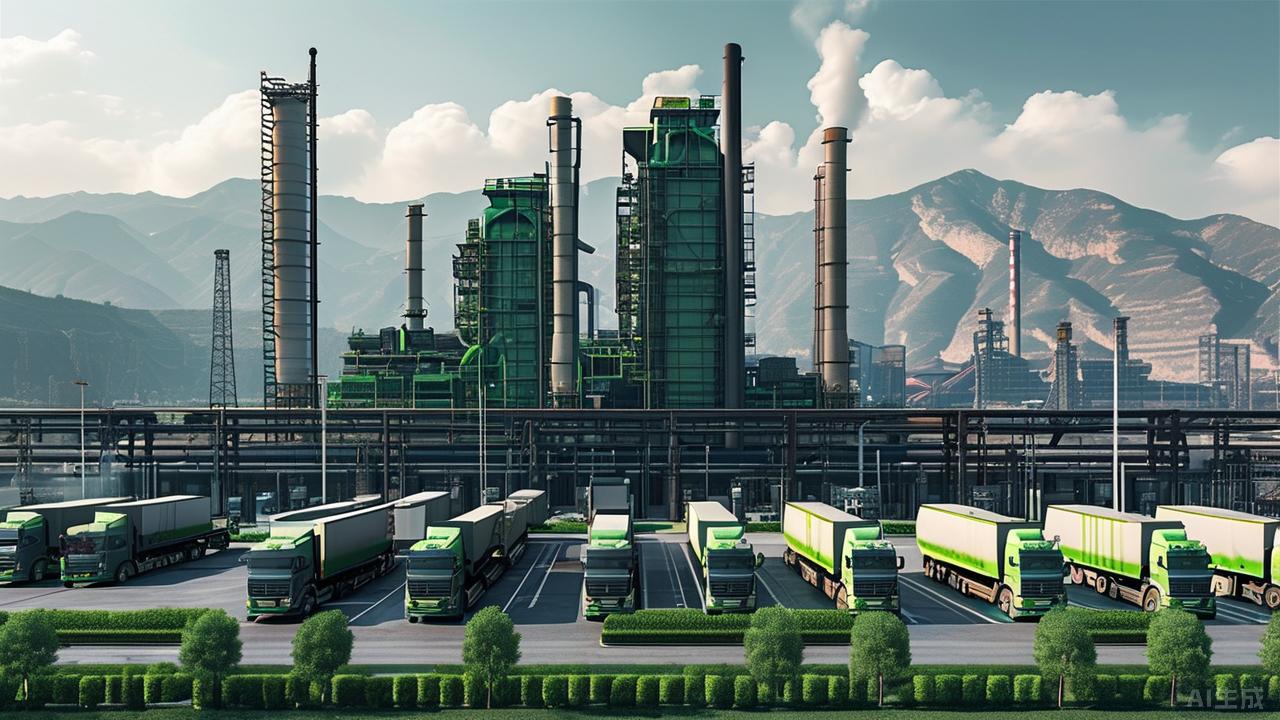
政策研究者特别指出,这种“应用场景驱动技术迭代”的路径,打破了“先有鸡还是先有蛋”的产业困局。当500辆氢能重卡已在大同物流干线常态化运营,市场需求反过来 *** 技术升级——正如跨省氢能干线催生出耐低温、长续航的第三代燃料电池系统。
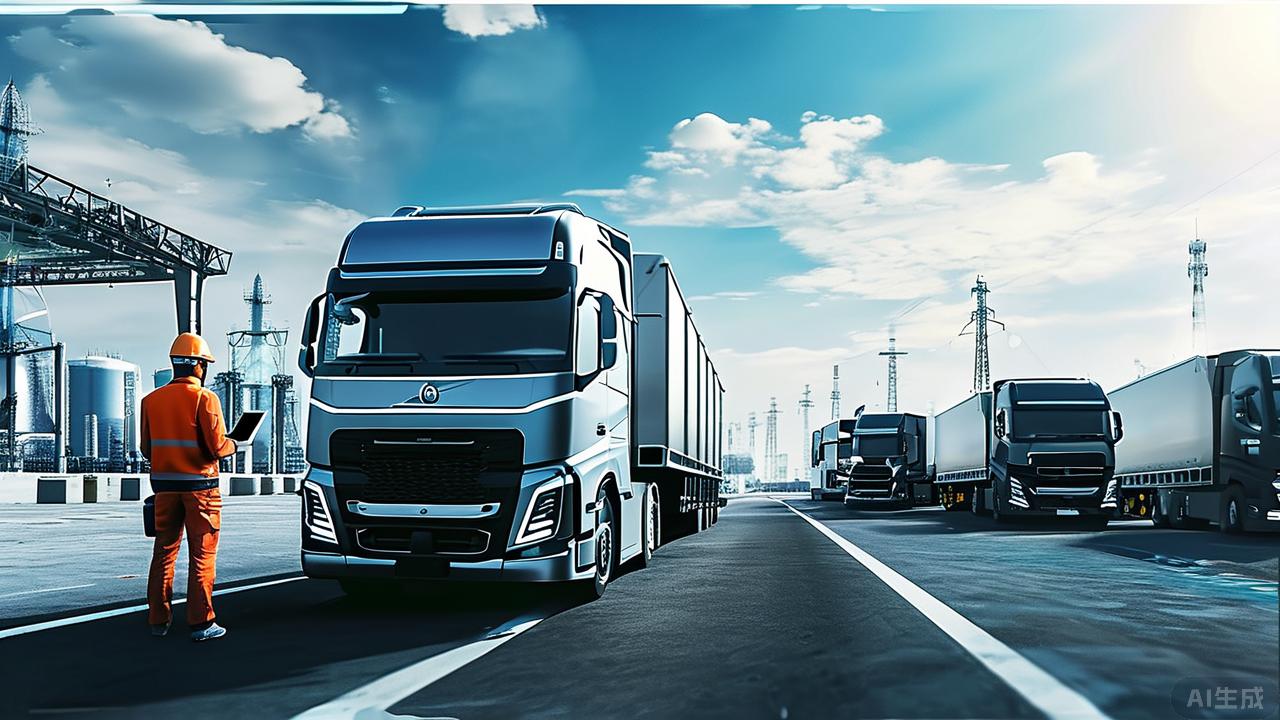
未来展望:氢能重卡的下一个爆发点
站在2025年的门槛回望,氢能重卡的进化图谱愈发清晰:产能规划正从5000辆向1万辆攀升,氢能炼铁、热电联产等工业应用场景加速融合。而在更宏大的蓝图中,大同经验或将复制到全国——佛山已率先探索氢能工业车辆在陶瓷行业的应用,试图打造“氢陶都”新名片。
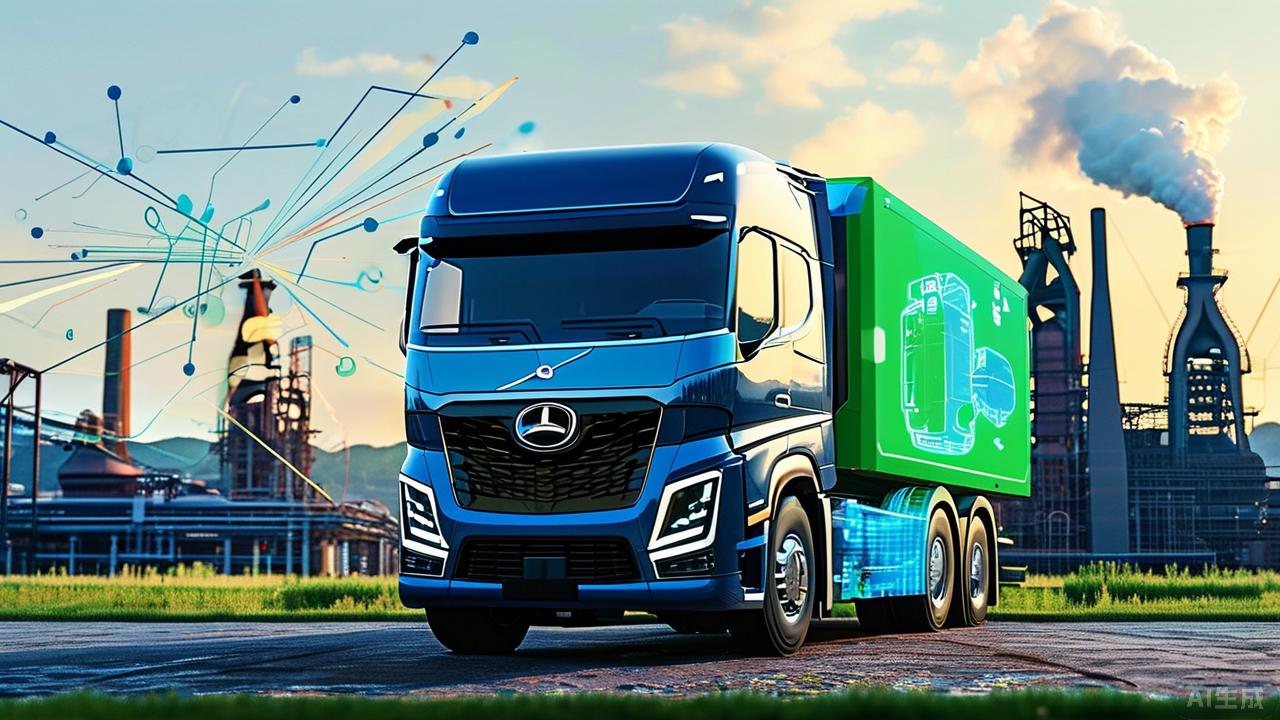
正如生产线上一枚小小的氢燃料电池,每一次化学反应释放的能量虽微,汇聚成流便是推动产业革命的澎湃动力。当环保理想照进制造现实,氢能重卡的故事,才刚刚翻开扉页。